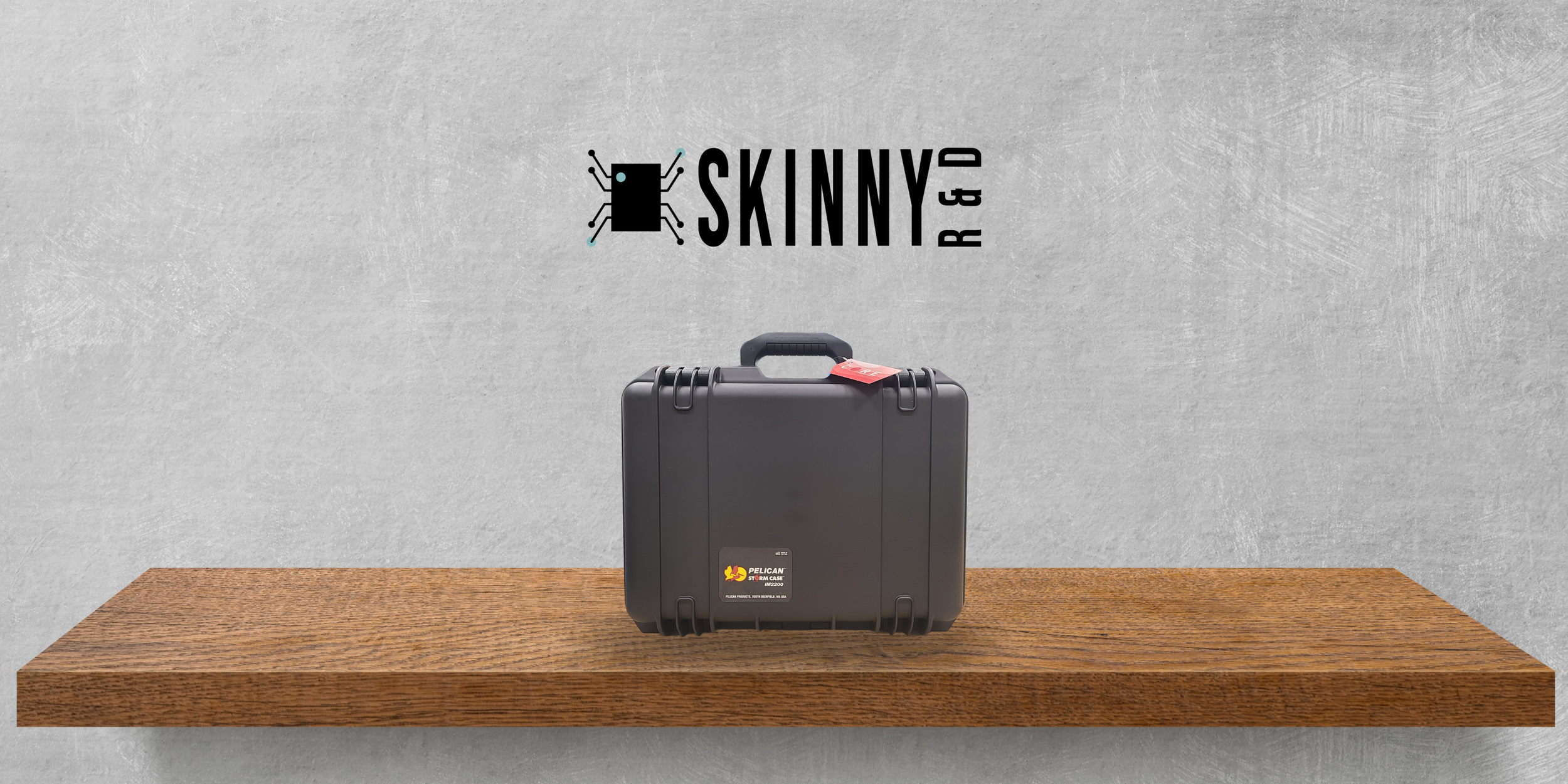
Engineered Protection
When transporting electronics, protection from particulates, impact, and water is essential, along with ease of use. A custom-designed electronics case addresses these concerns and more, ensuring optimal safety and convenience.
Brainstorming
Rapid Development
Assembly
FFF Printing
The Design Process
Since this case is fully custom, the first step in the project was to gather precise dimensions of all components to be housed within it. Each part was carefully disassembled from its external casing and digitally modeled to determine the optimal case size for the application. From there, custom mounting brackets were designed and the appropriate bolts, standoffs, guide rods, and wiring were selected to be approved by the client to ensure a perfect fit and functionality.
Material Selection & Assembly
Material selection is based on factors such as heat resistance, moisture exposure, and structural strength. For this project, several custom components, including the parts cover, needed to be designed and fabricated using FFF printing. Given the application’s requirements, ESD-resistant PETG was chosen as the optimal material, providing durability and electrostatic discharge protection.
The final box was assembled with the central stack being mounted on two guide rods through the front & back sides of the box. Custom mounting brackets were bolted into the case for several parts. These parts connected to two inputs and one output port. In addition to this, a custom part concealing lid was made to mount atop. This concealment cover features disassembly instructions to make swapping internal parts a smooth process.
The Final Product
The final product underwent thorough testing to ensure all components functioned properly before delivery. Once verified, the custom case was handed over to the client, meeting all design and performance requirements.